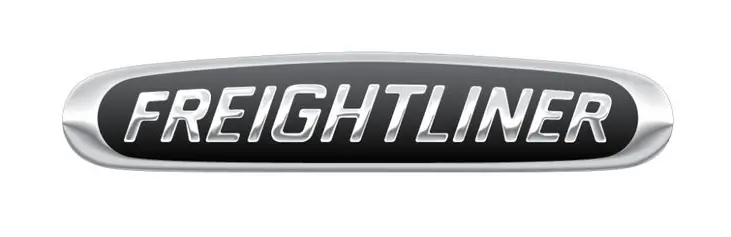
Freightliner (Daimler AG)
Freightliner trusted our team to implement multiple LEAN Sheet Metal Storage Systems in place of their old cantilever racks. With their new systems in place, Freightliner can now send LEAN Cartridges to and from their steel suppliers in place of wooden pallets, and then directly load full bundles into their fiber laser automation towers. From start to finish, they’ve streamlined their storage operation and become more efficient in getting cut parts downstream to other processes in their facility.
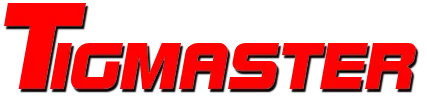
Tigmaster
Tigmaster is a cutting edge manufacturer offering welding, laser cutting, machining, waterjet cutting and much more. They pride themselves on quick turnaround times and having the most modern equipment and newest technologies available on the market. As they’ve grown, they found themselves buried in sheet metal which was effecting their production. Hear how they turned to Lean to create more floor space and have continued to invest in sheet metal storage racks in order to keep their shop clean and best serve their customers.
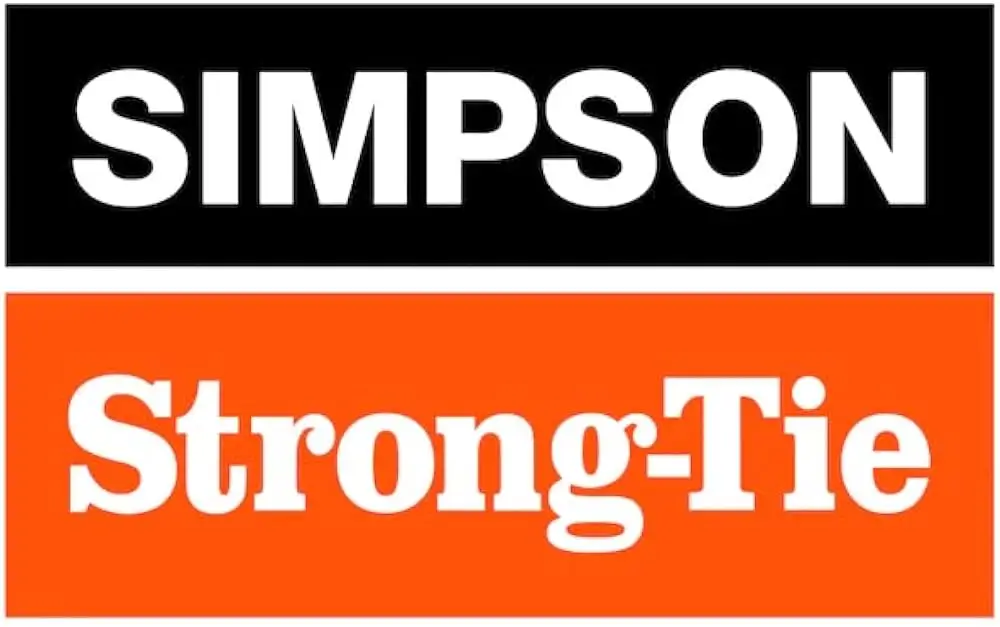
Simpson Strong-Tie
The integration of LEAN Safety Block Storage Systems created a seamless storage access point that improved the efficiency and productivity on the shop floor. Sheet metal secured in independent cartridges eliminates the potential of damaged material, reduces machine downtime, and will create cost-savings for Simpson Strong-Tie for years to come.
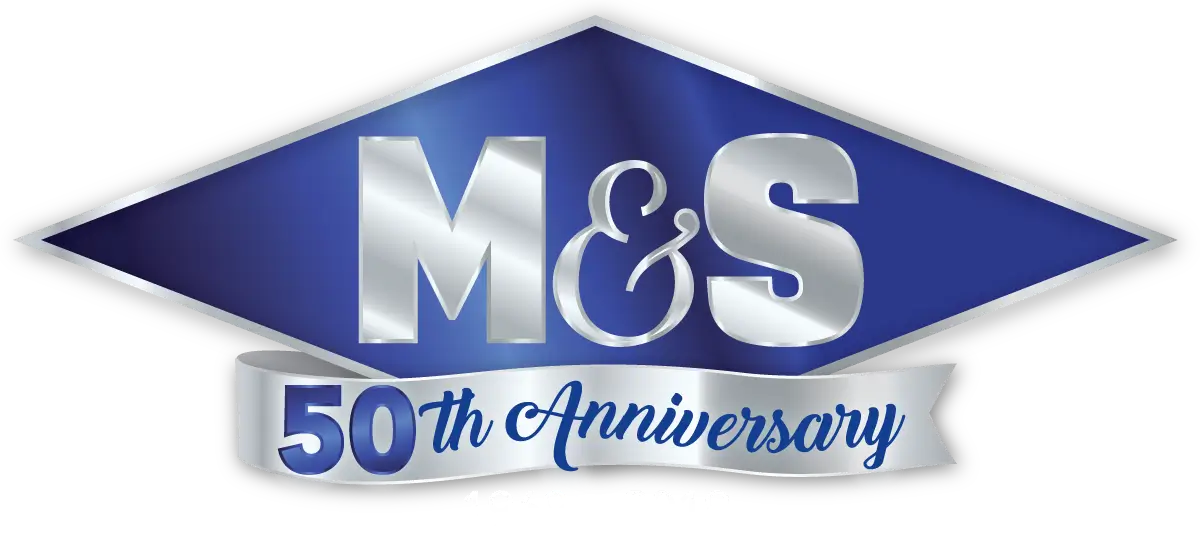
M&S Fabrication
New fiber laser? Buried in raw material? If so, you’re not alone… here’s a peek inside M&S Fabrication to show how they overcame their inventory challenges. After realizing how much time they were spending every day unburying the material they needed, they knew they needed to invest into their first touch points: raw material before it even hits the laser; and the results are outstanding!
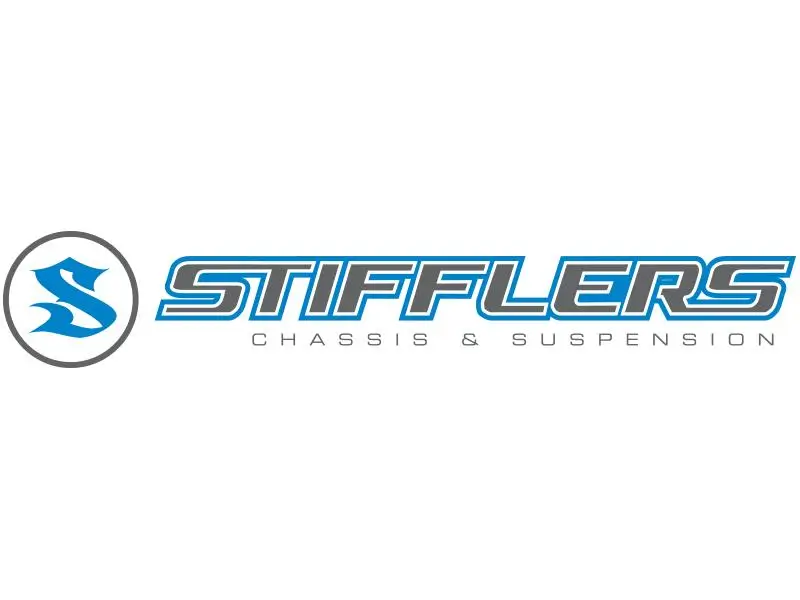
Stifflers Chassis and Suspension
Adhering to lean manufacturing principles is one of the many ways that Stifflers Chassis and Suspension finds great success in high-quality laser cutting and metal fabrication. After becoming buried in raw sheet stock for their high-speed fiber laser, they trusted Lean Manufacturing Products to provide a turnkey solution for managing their inventory with a reduced footprint and increased accessibility. Listen along as their Production Manager, Mike Simpson, explains how they operated before having LEAN’s sheet storage rack, and how they are now thriving post-installation – with newly created space, capacity, safety, and throughput. A big win for all.
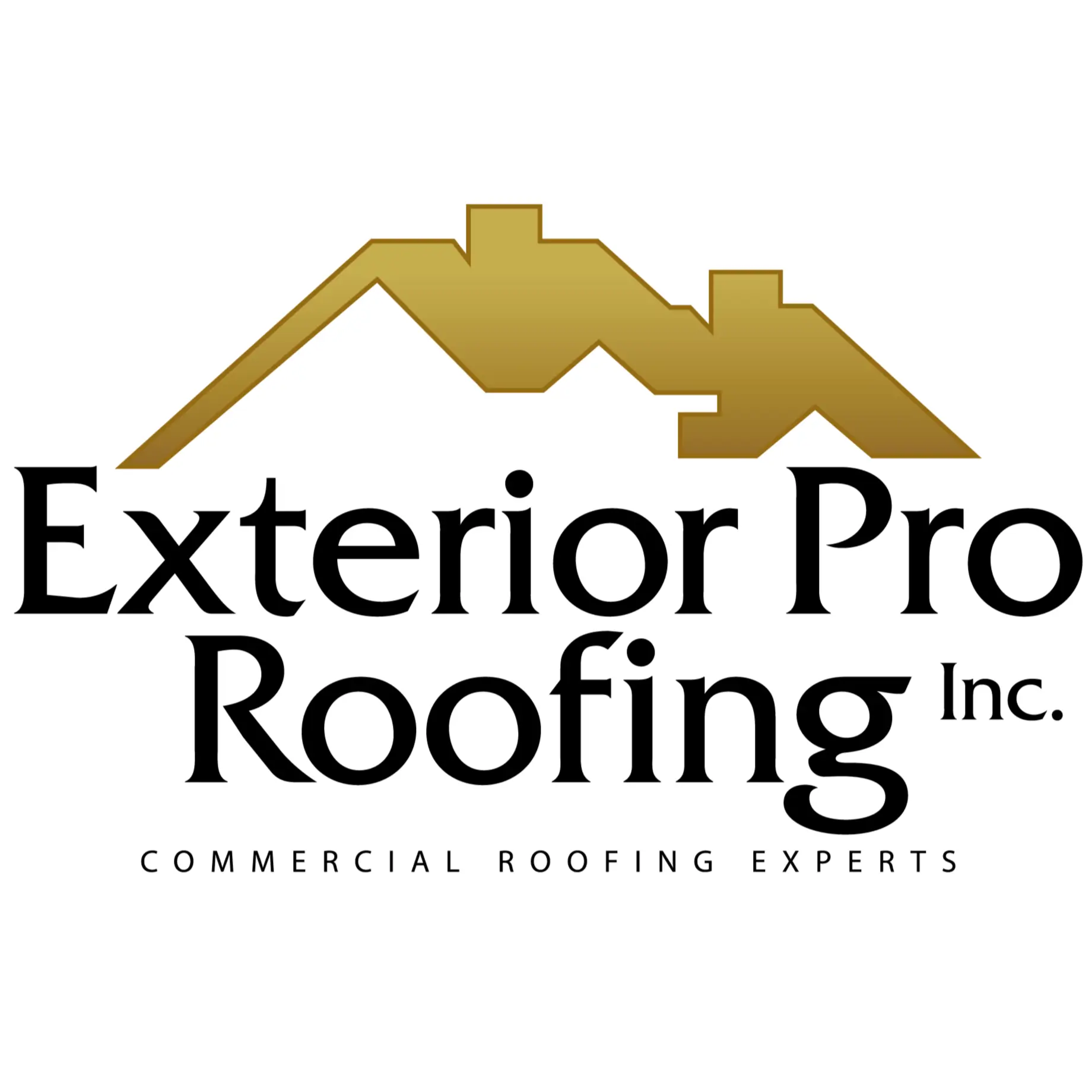
EXTERIOR PRO Roofing, Inc.
Is the investment worth it? In this short “Gear Review” video, Meet Aaron Perry, owner of Exterior Pro Roofing in Indiana. If Aaron’s space and efficiency challenges sound relatable, we would love the opportunity to create a similar success story!
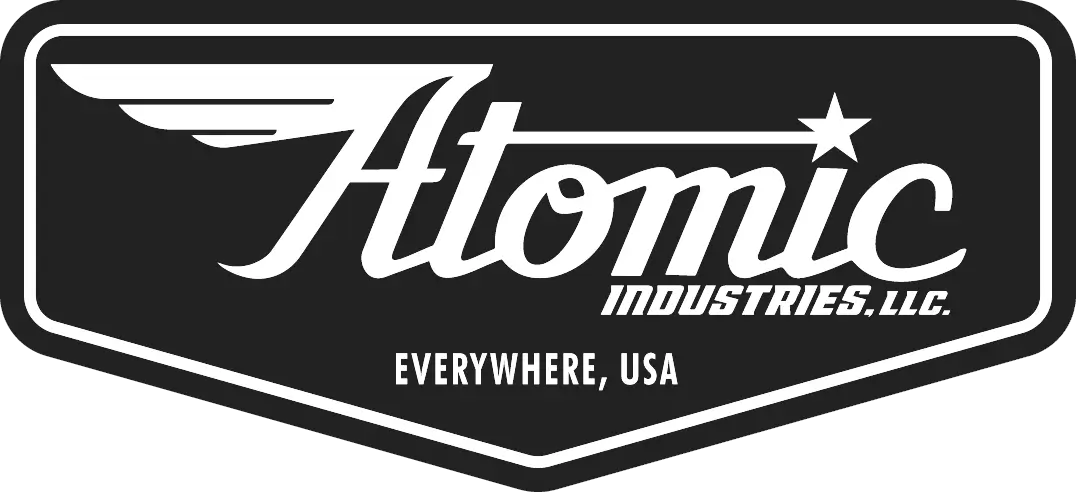
Atomic Industries
At LEAN, we’re incredibly proud to work with companies that continue pushing the limits of metal fabrication – such as Atomic Industries. We’re humbled to play an integral role in the efficiency of their premier fabrication facility.