Sheet Metal Storage Rack
Sheet metal storage and staging is an expensive challenge.
As new lasers and punching machines get faster, a space-saving, streamlined material handling and storage system is more important than ever.
The LEAN Sheet Metal Storage Racks keep raw metal material easily accessible, protected and secure and with a manual cartridge system, will immediately free up floor space, increase efficiency, improve safety and help you create a leaner manufacturing facility.
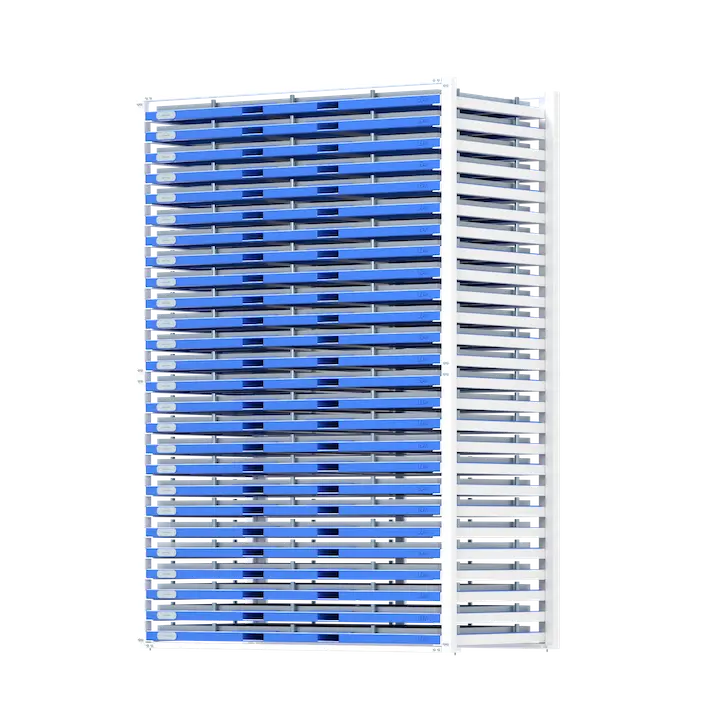